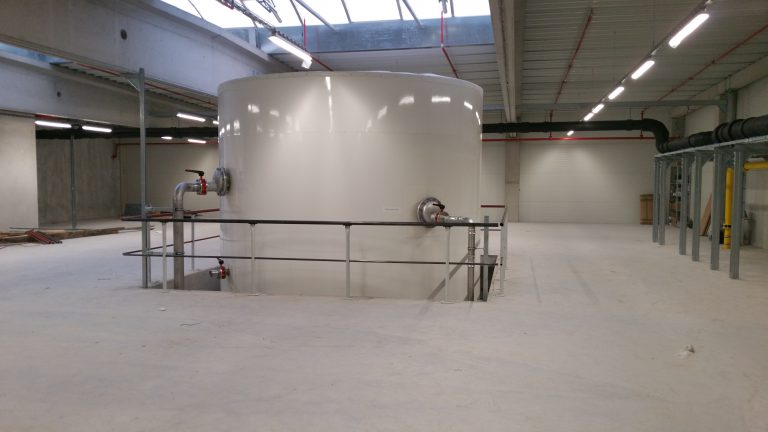
79 m³ hot water tank for Germany’s largest hotel laundry
The Haase hot water tank has a volume of 79,000 liters
The Greif Textile Mietsysteme company has set up the largest and most modern hotel laundry operation in Berlin, Germany. The aim was to incorporate latest proven technology and reclaim thermal energy were economically viable. This will greatly reduce operating costs and therefore ensure the most competitive operation..
Hot water costs of such an industry represent a major part in the cost structure. To reduce these it was decided to invest in latest proven technology together with a sophisticated energy concept. This step would result in a very efficient and cost saving process. The big advantage, due to the much lower processing costs , is that the factory could now be located much closer to their customers eliminating long transport time and costs.
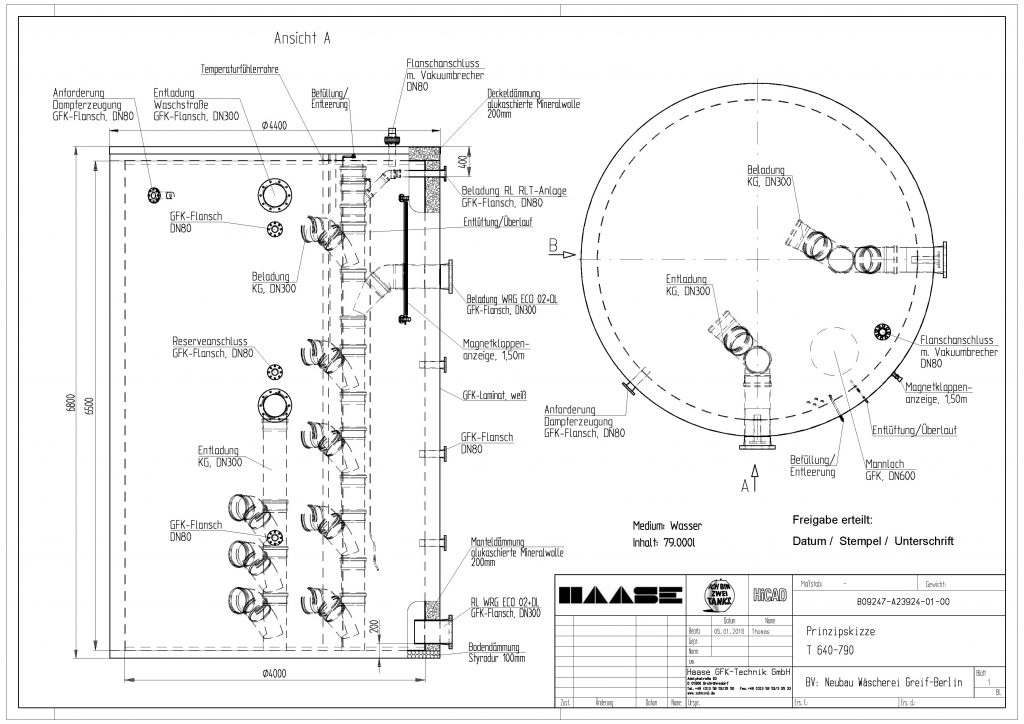
Heat recovery is an important part in reducing energy costs: Our 79,000l Haase tank is the center piece in the heat recovery system. It was designed to utilize waste heat from hot waste water coming from the washing machines and steam boiler, the air compressor system, flue recovery from steam boiler, as well as recovery from the building heating system. This recovered energy is then used for the continuous hot water supply to the five industrial washing machines.
The first process is the heat recovery from the hot wastewater. For this a 10,000l Haase tank accumulates the remaining thermal energy from the hot wastewater. This hot waste water is then pumped via a cross flow heat exchanger to heat up the incoming cold water using a variable pump to control the counter flow. This process increases the cold water temperature generally from 12°C to 45 °C , before it is transferred to our central thermal recovery tank. There the temperature is increased to 60° from other recovery sources.
In the first step, the wastewater is collected in a 10 m³ Haase flat-bottom tank. The waste heat from the wastewater increases the temperature of the process water from 12 °C to 45 °C before it flows into the hot water tank (79,000l). In the storage tank, the process water is then heated up to approx. 60 °C using various heat sources.

The two air compressors constantly create heat at approx. 65 °C. This is transferred to the top part of our central tank.
In the middle part of the tank waste heat with approx. 60 °C is fed in from the return of the building heating (300 kW). The lower section of the storage tank is loaded with heat from the flue recovery from the 4 MW steam boiler, which is used for various processes in the laundry.
After the system was commissioned it was confirmed that the heat recovery functions as designed resulting in major cost savings since it increased the water temperature from 12 °C to approximately 60 °C. This eliminates the use of a steam boiler for this temperature increase.
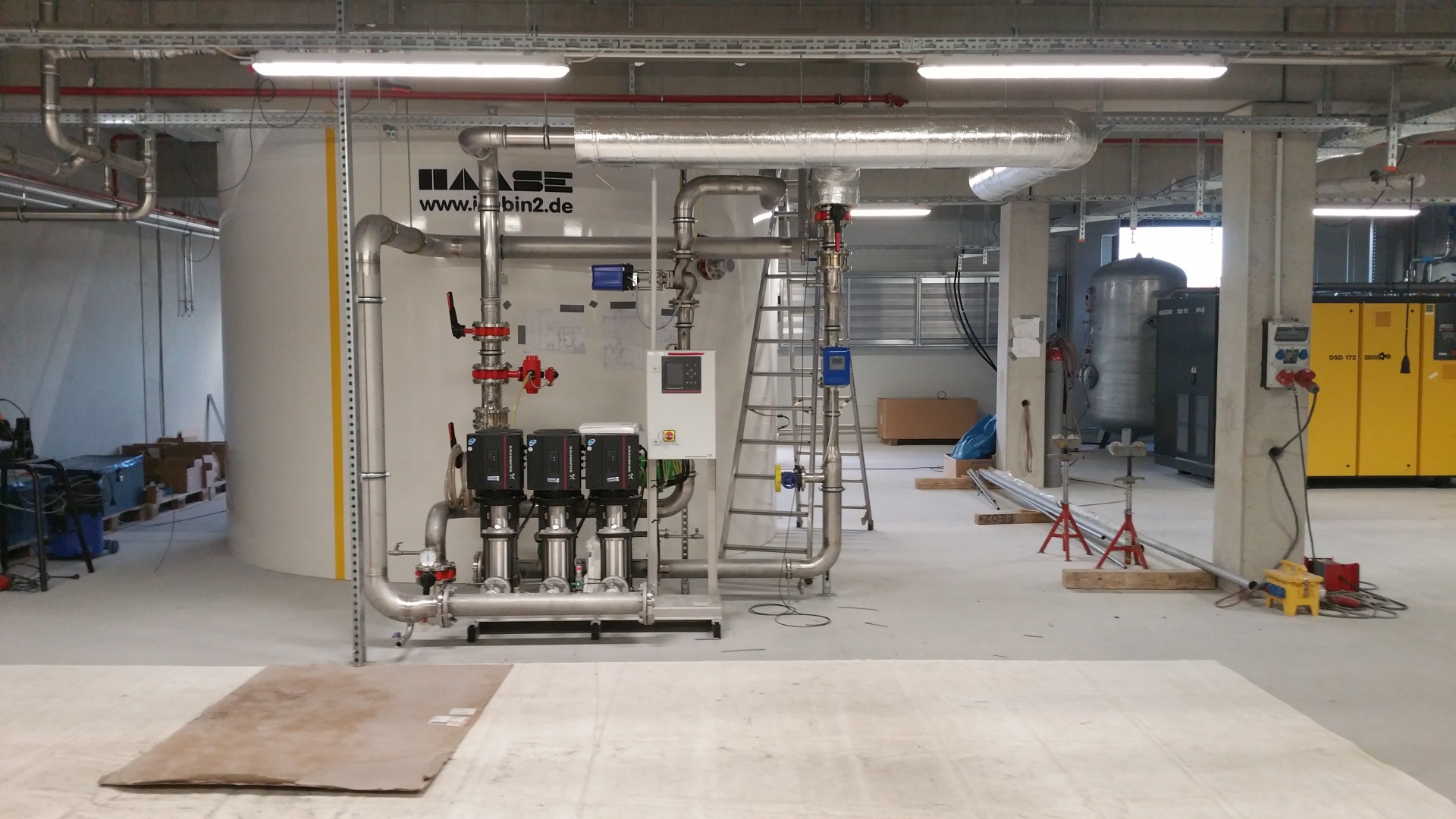
Just a few weeks after commissioning the system, it could be confirmed that the saving targets have been met and even exceeded.
The steam boiler operates now with an efficiency of 95 %. By using the waste heat from the boiler and the compressed air generators, around 17,500 kWh per day can be saved; another 1,500 kWh/d results from the use of the return of the building heating. In the next stage of expansion, the waste heat from the boiler should raise the hot water temperature to 55 °C. The result of the thermal recovery system are daily savings of around 25,000 kWh.